“I’ve just bought the anodising kit. I’ve been inspired by this artist who uses amazing pastel colours and has made a deconstructed head with the eyeballs coming out. His colours are phenomenal – they just look so good, so I’ve based this year’s Paint Haus colour pallet on his designs.”
That was pretty typical of one of the topics I chatted with Rob Quirk about. When I went to visit, Rob was building a hardtail MTB frame which was destined to be the star at the 2021 Bespoked show and he had decided to anodise the parts for it to give it a unified look. He figured the best way to get the finish and depth of colour that he wanted was to do it himself, so he was busy teaching himself the techniques necessary.
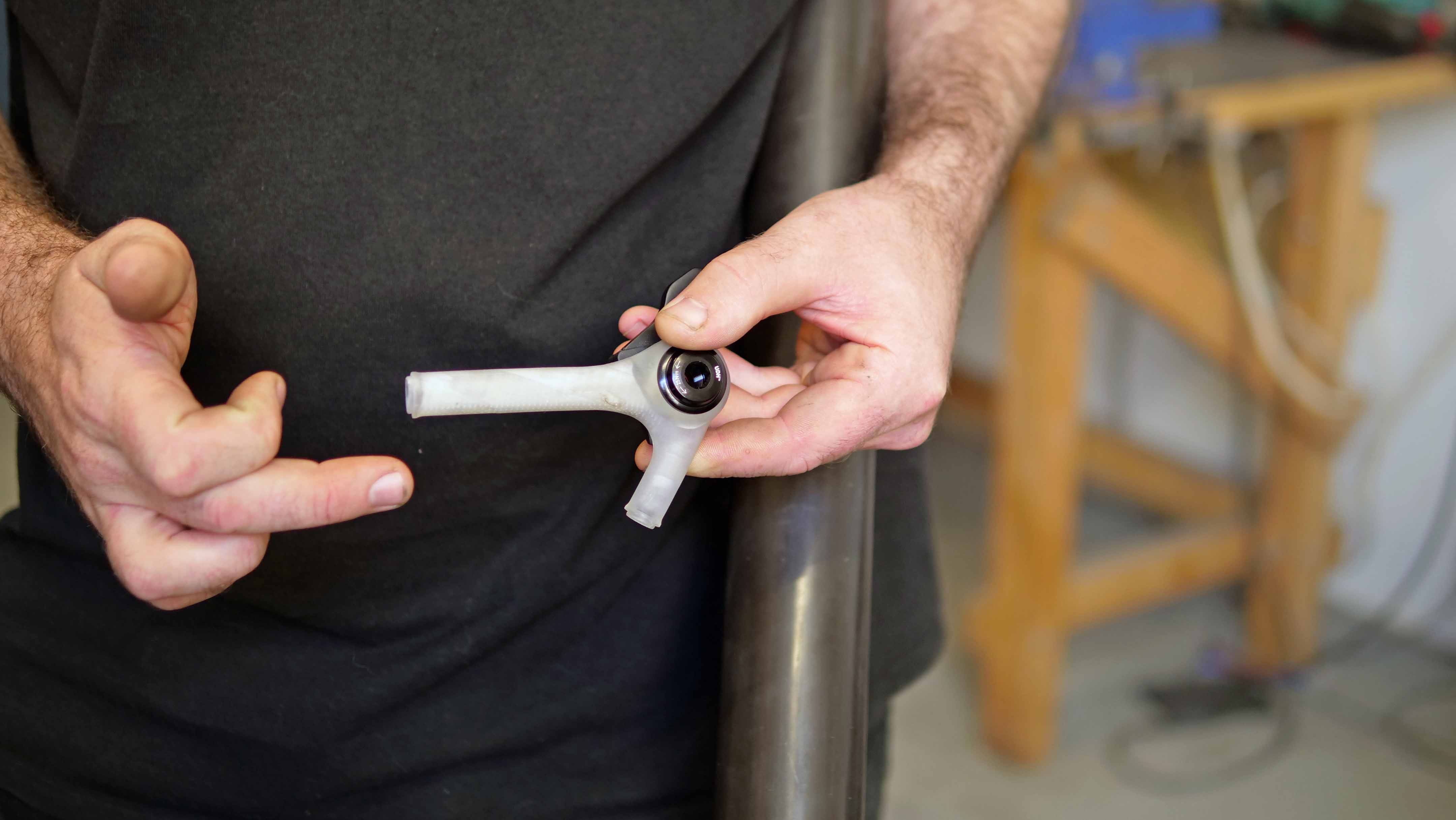
That was a common theme which ran through a lot of our conversations. Rob had found the careful balance between knowing what he could (and should) do himself and which parts to sub-contract out. As I walked into Rob’s workshop, one of the first things that caught my eye was a small collection of 3D printed parts sitting on top of a heavyweight metal table. Rob normally works with Columbus steel tubing, but for his latest build he had been prototyping some new dropouts and a top tube/seat stay/seat tube junction, which he was going to have produced in 3D printed stainless steel by an external contractor.
“I'm contracting out the bits that are a pain in the ass to do myself” was how he put it. The new dropouts and seat tube cluster have a number of big advantages “they will make a lighter set-up, they’re stronger as they distribute stress better and they enable me to build a frame quicker”. In my opinion they look absolutely fantastic too, but Rob has previously been quoted as saying that a bike is “a tool, not a jewel”.
I asked Rob how he’d initially got into frame building. He’d been studying for an MA in Research Architecture at Goldsmiths but for a bunch of complex reasons including some mental health issues, he had decided to drop out. Building custom bike frames became both his means of generating an income, but also a type of therapy to deal with his self-described “quarter life crisis”.
“There’s a really good book by the academic Matthew Crawford called ‘The case for working with your hands’ where he suggests that there is a rise in depression in modern societies because people don’t work their hands anymore. They don’t see the fruit of their labours. I realised this and obviously I had a deep obsession with bicycles, like a lot of people do. So I booked myself onto a Bicycle Academy course and it ended up being therapy as much as it was practical training.”
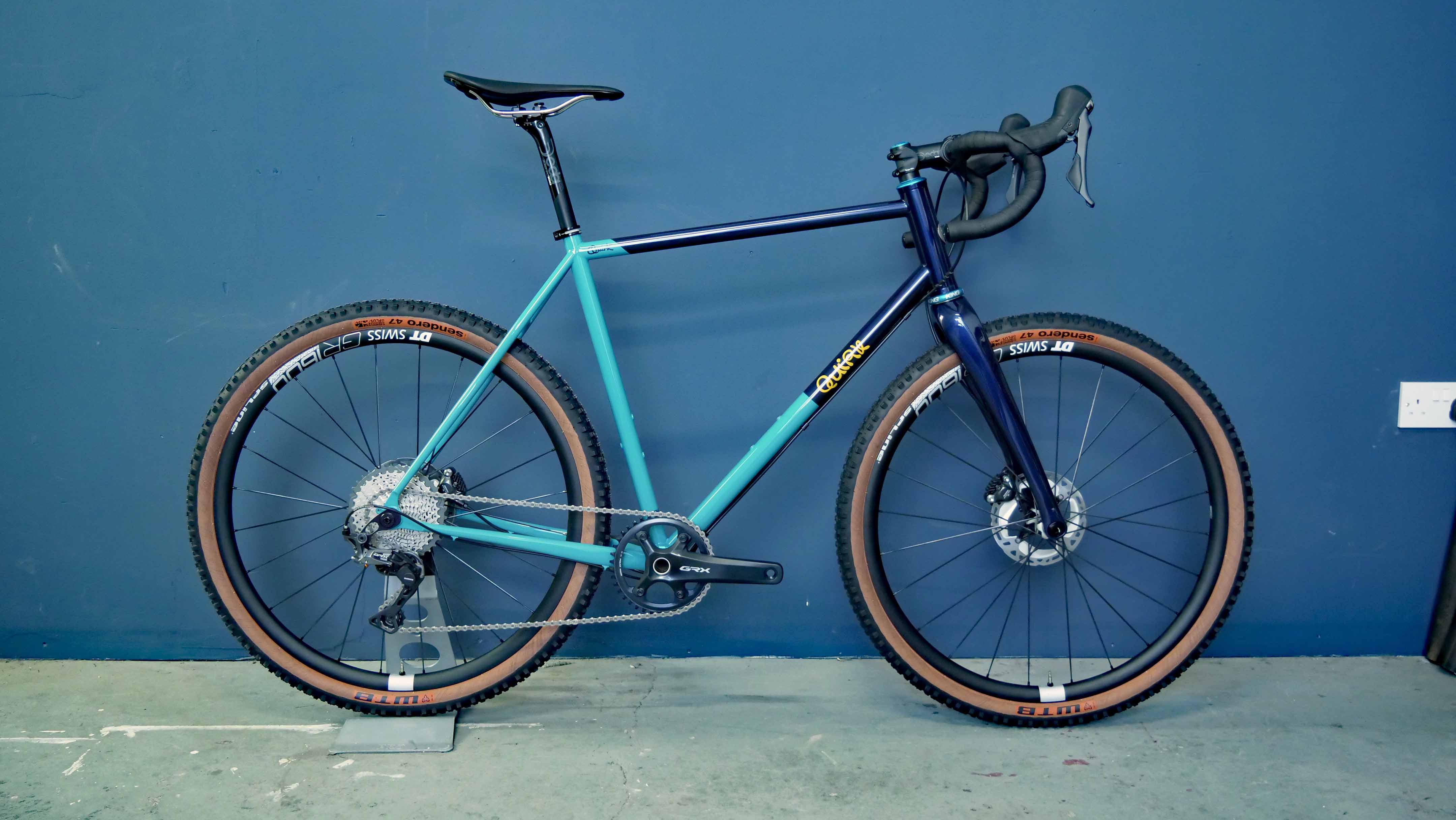
Since he first set up in March 2015, Rob has gone on to win four awards at Bespoked. Like all custom bike frame builders, he can turn his hand to pretty much anything bicycle-shaped “I’m a custom frame builder after all”, but he continues “ I’m definitely seen as a builder of off-road machines rather than pure road bikes.”
Rob currently offers five designs:
· Durmitor – an endurance road frame named after a peak in Montenegro. It was designed for and tested in the Transcontinental race.
· MamTor – an all road/gravel frame named after an iconic hill in the UK’s Peak District.
· Kegety – an adventure gravel frame, named after a pass in Kyrgyzstan which riders attempt in the Silk Road Mountain Race
· Overland – an adventure/bikepacking frame. It was designed for and tested in the Atlas Mountain Race
· Superchub – an XC race hardtail, which Rob will be using in the next AMR in 2022.
The unifying factor in all of these frames is that Rob has generally built the prototype with a specific event in mind. That might be 4000kms across Europe on the TCR or tackling some of the brutally rocky “gravel” trails in the High Atlas mountains during the AMR. Each time he has come back with a frame which has been pushed to its limit and with design iteration ideas firmly imbedded in his brain.
When you first walk into his workshop, located in a very trendy and bohemian part of east London, you will probably notice one thing – the remarkable lack of machinery. My preconception of a frame building workshop would be that it was full of lathes, milling machines and perhaps a small forge. But when I asked Rob about this, he explains that he does things slightly differently. Rather than machining the appropriate shape of mitre into the end of each of the tubes that he uses to construct a frame, he uses a belt sander.
“I used to machine. I used to do mitres on a mill. When you’re using the mill you have a holesaw and a cutter. You set up your mill, you put the tube in a clamp and you go down and the mill is cutting. You might also have a horizonal mill which is cutting. But there are issues with this. First of all, it only cuts in one direction, so it’s always pushing the tube in one way. The teeth can get caught. It twists the metal. You have to cut it very slowly as the tubes are so thin that if you feed it too fast the teeth will just grab it and it would mash the tube, so it has to be done slowly. Changing angles becomes difficult. With a belt grinder you can very quickly and easily change the angle and the process is much faster. If you get everything set up right, a belt grinder will be faster and more accurate, with less time spent correcting errors and imperfections. The only thing you have to watch out for is heat build-up (which can change the structure of the tube), plus the noise and dust that the belt sander creates.”
One of the things Rob is justifiably well-known for is his paint finishes. “When I first set up, one of the issues I had was a lot of time customers knew what they didn't want in terms of paint schemes but they didn't know what they did want. Because of my background, as I trained in art and design, design language comes naturally to me. Being able to describe, and having knowledge of, finishes and colours and having knowledge of how to apply them is just something I've been trained in”
Rob has set up part of his business to specialise in paint scheme design, Paint Haus, so I asked him how it worked “Paint Haus was a way to first of all, offer a range of designs, in a range of colours, that communicated the Quirk brand and with finished frames that were recognisable as belonging to Quirk. So, part of it was branding and identity. I give my customers a choice of finishes. People can pay for upgrades to get more advanced finishes, but my aim was to provide something that was a good starting point. In order to keep prices reasonable, we have set designs. We have about ten colours that the whole range of designs are built upon.”
This led really neatly on a conversation about pricing. Rob explained how his pricing structure was set-up “Something I found really frustrating with other custom builders’ sites was that everything was POA [price on application] or my other issue was like when you go to a restaurant and they have everything on the menu, about a million things, and you’re overwhelmed with choice. I wanted customers to be able to come to my website, look at the price and know that the price included the frame, forks, Chris King headset, paint finish and custom geometry. There are some upgrades that we offer, but it’s not like a smorgasbord of a million choices.”
We finished off our conversation by me asking Rob where he saw himself being in 3/4/5 years down the road. His deadpan answer was “Spain”. Despite how relatively warm and sunny London is compared to Newcastle (where Gravel Union UK is based), Rob wanted to head further south. But also “I'm kind of on a little push to try and become a bit more high end. Not necessarily exclusive, but I think I currently make quite practical bikes. When I say high end, it's not an exclusive, expensive way, but just try to mix up what's going on with the bikes. Not necessarily cutting edge but bringing in more interesting parts. Things like custom shifters for the Superchub with very slender 3D printed magnetic switches. I’d like to start integrating more things like that into my builds. I’m going to be bringing in integrated cable routing and 3D printed parts. I’m going to try and make the little details go further. Titanium is on the horizon too. I’ve started playing around with the material side of already, but I want to get stainless steel really ‘bolted down’ first”.
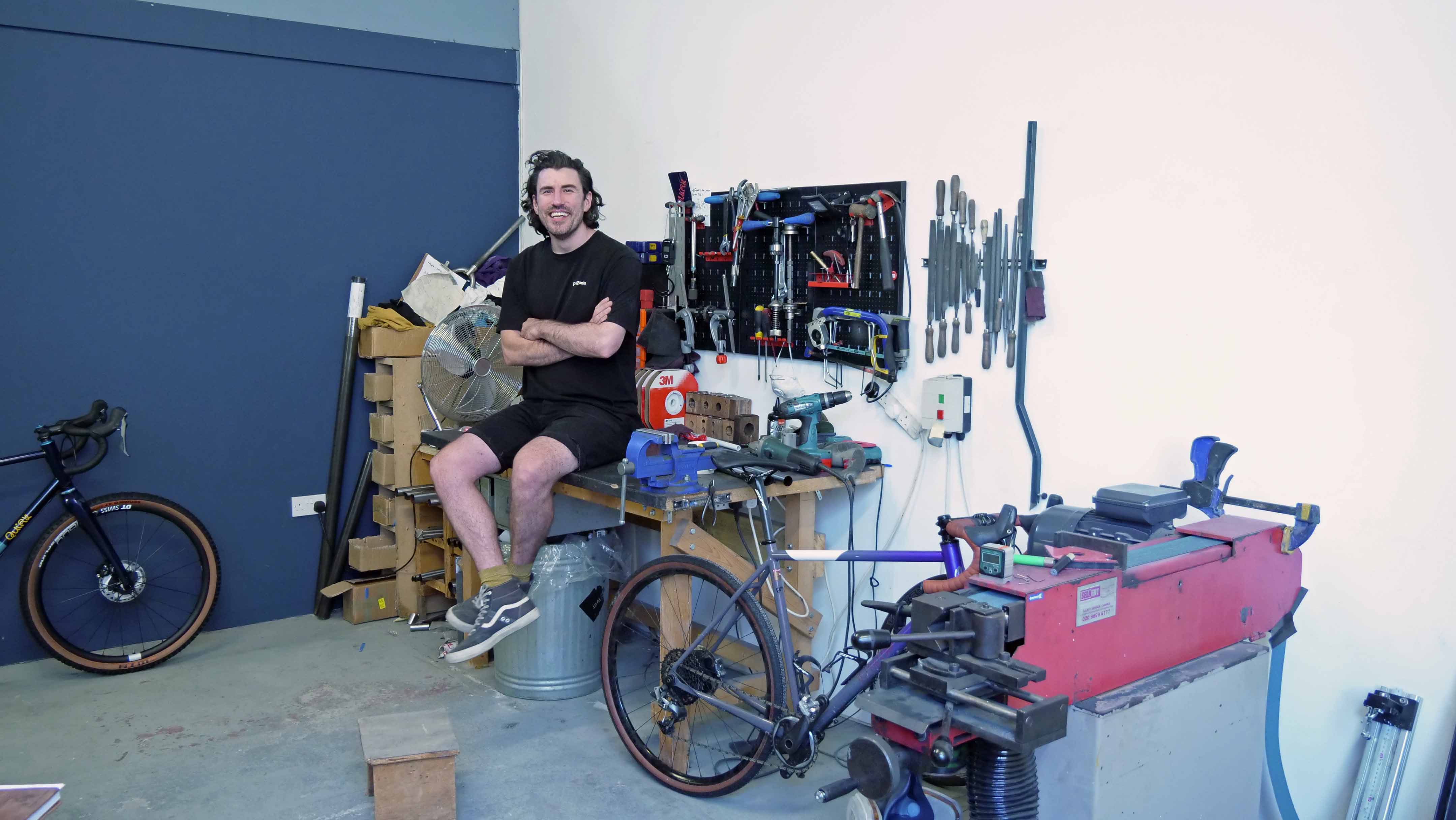
Over the course of an afternoon with Rob, we managed to generate more than 25,000 words of interview copy, so this piece is really just the highlights of what we talked about. Rob’s passion for doing things ‘properly’ and making sure that quality was his top priority shone through. But also, his love of pushing the boundaries, trying new technologies and seeing how far he can take his frame building was also obvious. We can’t wait to see what direction he takes Quirk Cycles in the future.
If you’d like to find out more about Rob’s custom frames, check out his website here and it you’d like some more inspirations and stories behind the build, check out his blog here.