“The VCLS seatpost is the longest running component that we have at Canyon”
“The VCLS seatpost is the longest running component that we have at Canyon” said Michael Adomeit, Canyon’s Engineering Team Leader, when we chatted to him about it recently. “We’ve been selling it since 2013, but it’s still a modern concept. It’s had a few minor tweaks to the design, for example when we introduced the internal seatpost clamping mechanism to the Grail we had to make the seatpost slightly longer, but the essential design was not touched”
In the bike world, no matter which genre, most high-end products are regularly tweaked and updated. This could be for functional reasons or because technology has moved on. But also from a commercial perspective, product updates are essential for keeping customers interested and sales up. So, for Canyon to have used essentially the same design for a decade is remarkable. “It could be considered an evergreen product” Michael continued.
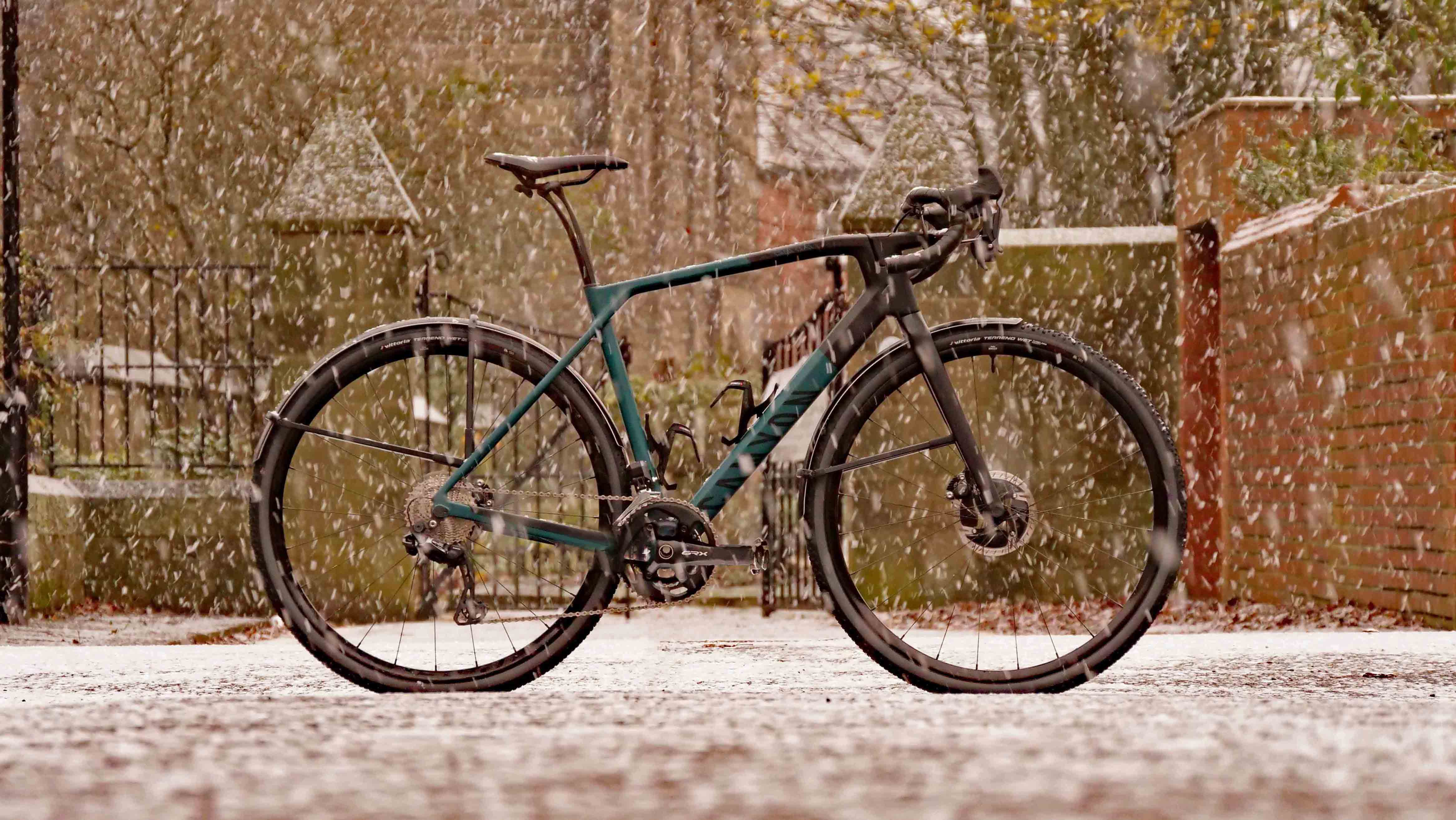
VCLS stands for Vertical Compliance Lateral Stiffness and is the Holy Grail of products designed to add comfort to the ride of a gravel bike. Or any bike for that matter. What Canyon aspired to achieve with the VCLS was comfort in the direction that the rider wanted it (essentially up and down), but stiffness in the direction where they needed it (side to side). The post, which weighs a scant 240g, is constructed from two carbon-fibre ‘leaves’ which are bolted together at the base of the seatpost. They are also joined at the very top where they attach to your saddle, but in the middle section they are free to move forwards and backwards independently. The total movement is around 20mm. That might not sound like a lot, but it’s surprising how much comfort such a small amount of “travel” actually adds.
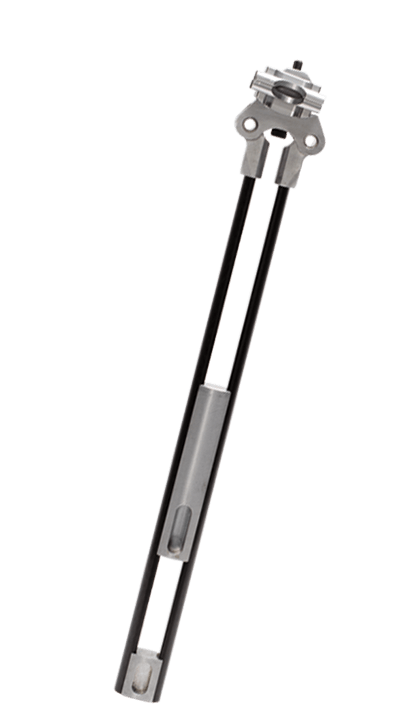
Prototype seatpost image courtesy of Ergon
“They were about to skip the project as they were not convinced that it was commercially viable.”
Canyon was created originally by brothers Roman & Franc Arnold. Franc later left Canyon and went on to set-up component manufacturer Ergon. When I asked Michael about the origins of the design for the VCLS seatpost, the relationship between the two companies soon cropped up in the conversation. “Ergon is very well known for their ergonomics already – it’s part of their name after all. We [Canyon] did some collaborations with them – mainly grips and pads and ergonomics related parts. But for the seatpost, Ergon recognised that there was a need for technical solution, instead of just trying to get comfort and better ergonomics via the padding of the saddle. They collaborated with an engineer from the Fraunhofer Institute and they came up with the design for the first prototype. The first version was quite “engineering driven”. It was OK function-wise and it confirmed the approach, but in the end they decided it was not a product which could be taken onto mass production. They were about to skip the project as they were not convinced that it was commercially viable.”
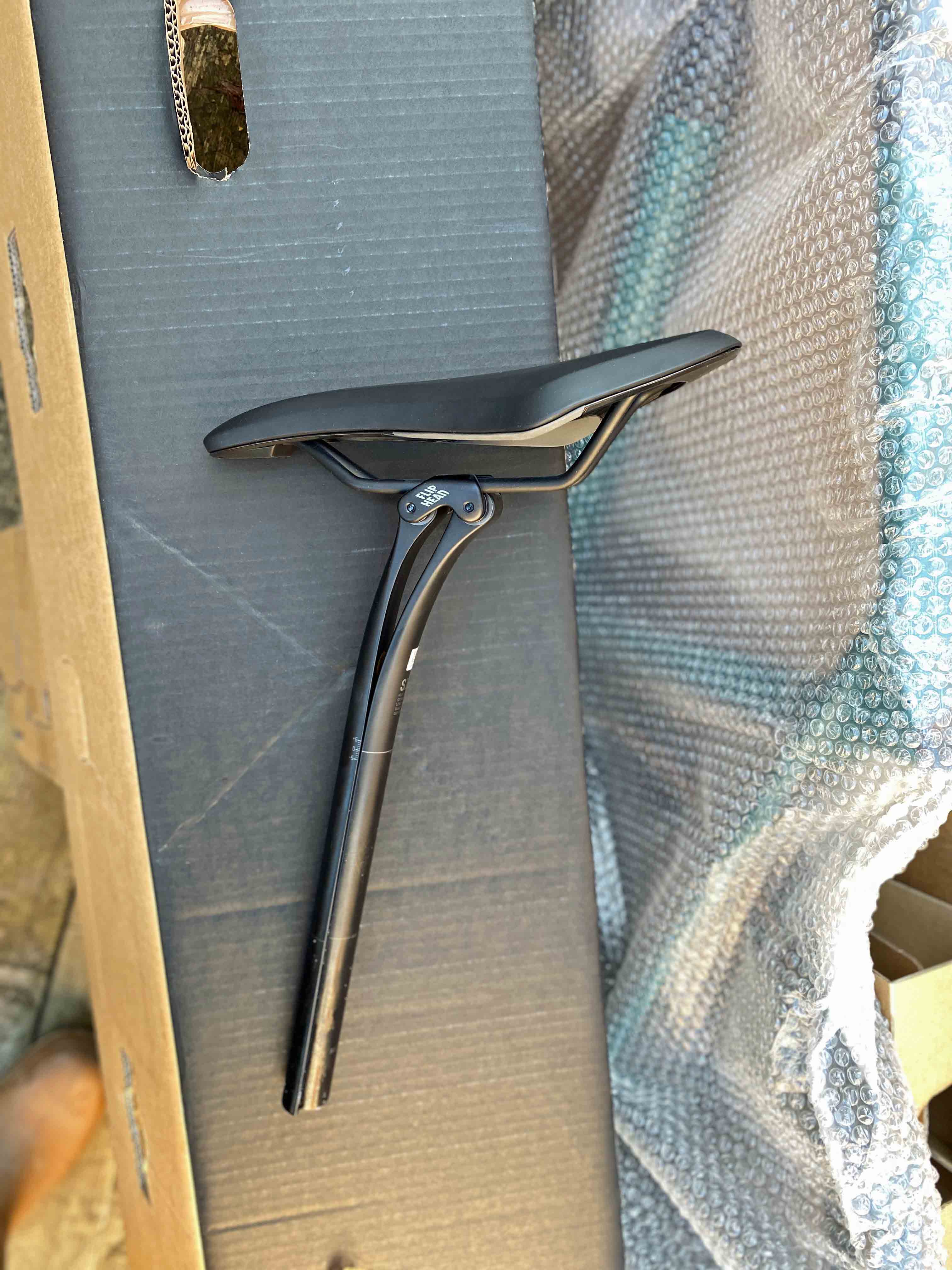
“If you look at how the VCLS seatpost looks today, it’s much different to the prototype design, but the basic principle behind it is still the same.”
Michael continued with the story “At that time (around 2009-10) Canyon and Ergon set-up a collaboration. Ergon knew that Canyon was very design-driven and we’re well known for our carbon manufacturing expertise. We also brought in other parties such as the Institute for Composites and the University of Applied Science, who we also use to develop the test rigs for Canyon’s test lab. We brought them in for testing and validation of the concept. Our task was to “make it nice looking” with less obvious engineering and more design, but keeping the comfort and compliance properties of the original design. This was one of the first big development collaborations between Canyon and Ergon. The collaboration was very successful and if you look at how the VCLS seatpost looks today, it’s much different to the prototype design, but the basic principle behind it is still the same.”
We talked next about the design and testing process that Canyon & Ergon went through. “The initial prototype was created using a “pull-trusion” process where the carbon fibre leaves were extruded.” Michael told us “This allowed us to automate the process, but it meant we couldn’t alter the properties of the leaves along their length. This introduced some potential weakness in the prototype. The design means there is high bending force along the length of the leaves, but with lower loads at the upper parts and higher loads at the lower parts, so it’s good if you can have the opportunity to adjust the wall thickness and the carbon layup over the length. This was something that Canyon brought into the design and today the parts are created using the same process we use for our carbon frames and forks. This gives us bigger freedom regarding the design and allows us to adjust the properties of the carbon over the whole length of the profile. “
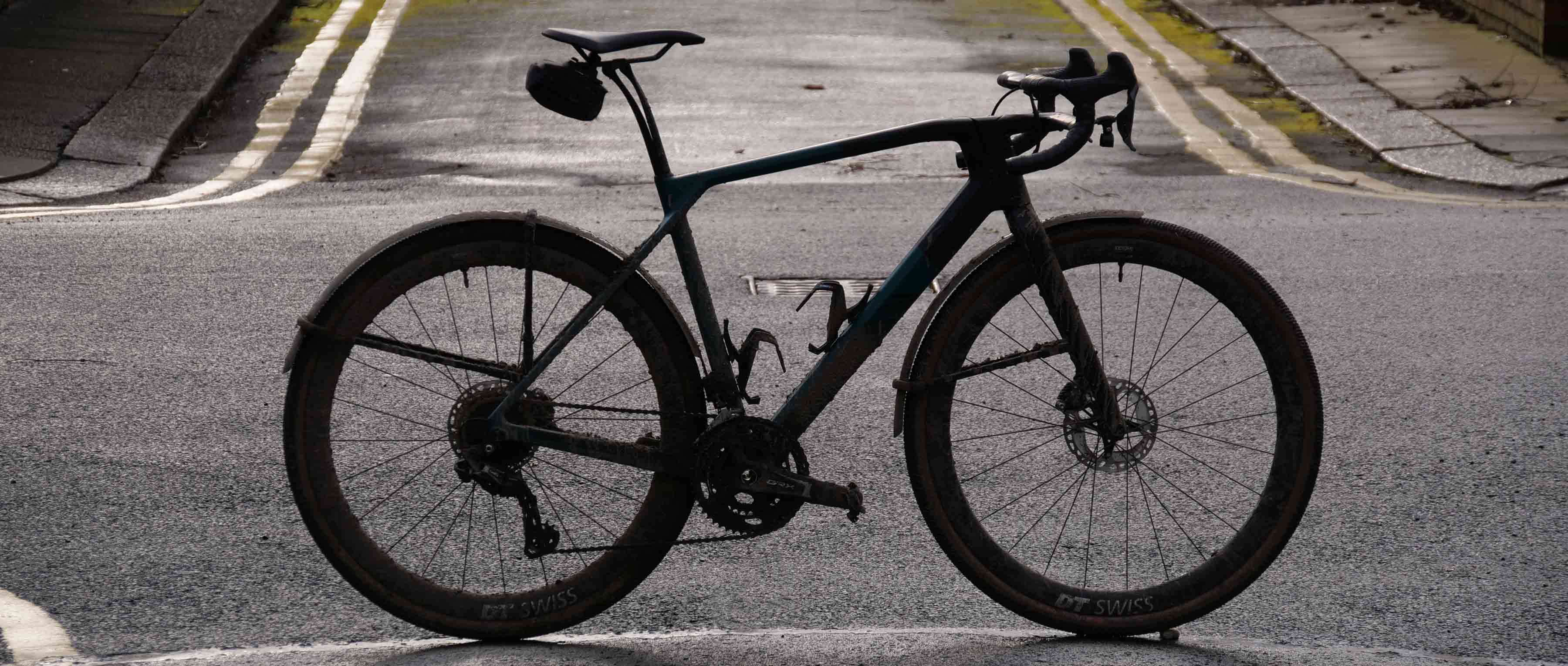
“You know, when something is so successful, you don’t always feel the need to further improve the design. But maybe in the future, with the design of bikes changing so much, then there will be more need to improve and to optimise our concept”
Michael continued with the story “When we’re designing a new component, we always think about some standard design criteria – weight, comfort, stiffness, aerodynamics and design of course and we always try to find the best compromise between these. For the VCLS seatpost, the issue of strength was a big headache for us at the beginning. Passing the static overload test for a seatpost is really challenging – for our testing we wanted to significantly exceed the requirements of ISO4210 standard and initially we had some failure in the prototypes, so we used Finite Element Method analysis to optimise the design. We used our partnerships with research experts in order to optimise the parts where we had experienced failure during the testing process and this went really well. We considered offering different versions with some adjustability built in to allow the rider to tune the level of movement, but it wasn’t practical when considering ingress of dirt for example, so the final design was simplified. The different versions of the seatpost that we offer have proved to be extremely popular with our test riders and our customers."“
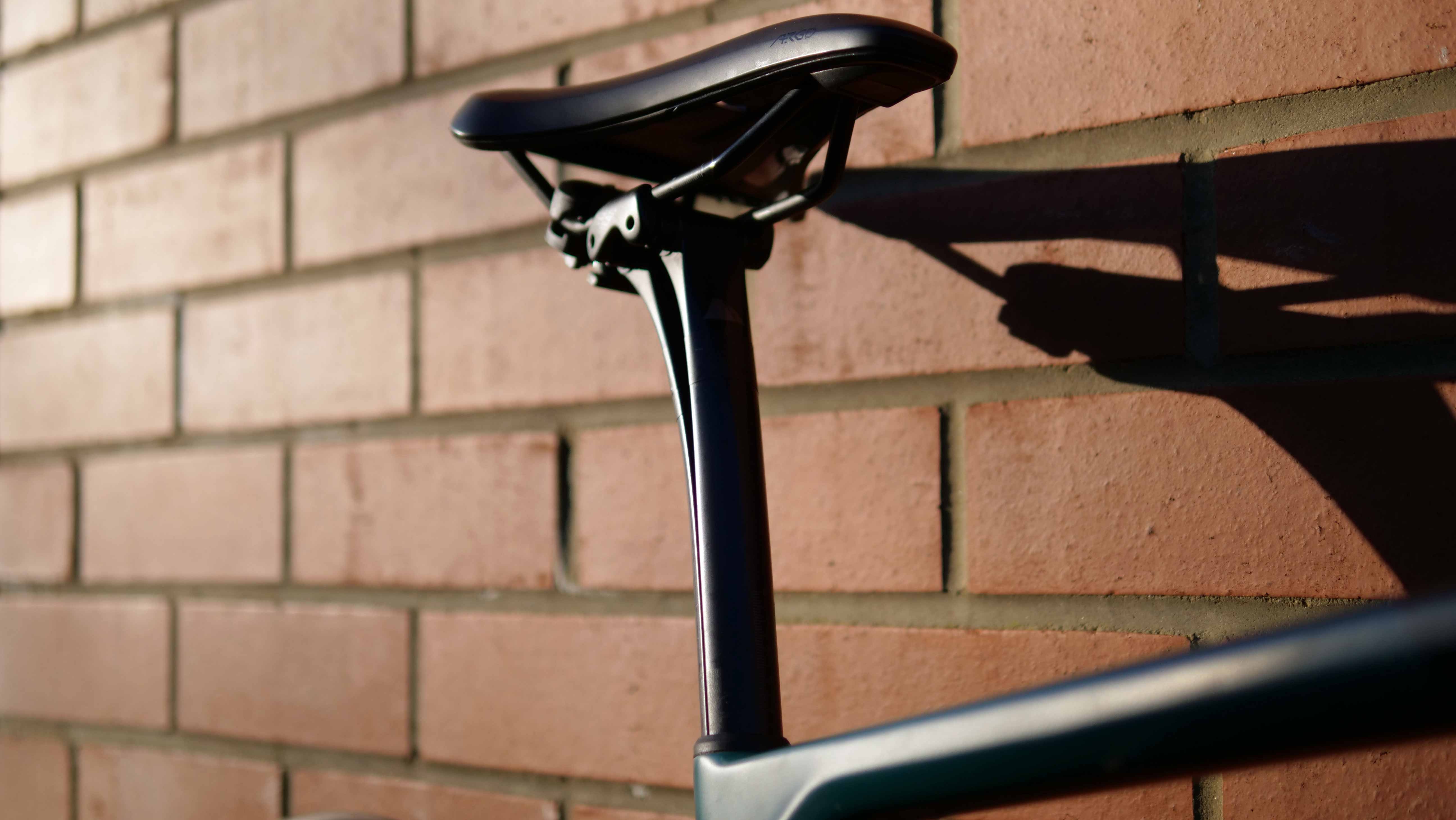
“There has not been a single failure of production VCLS seatpost that I know of”
Next, we discussed the potentially fraught subject of product issues or failure and what Michael told us was pretty incredible “As long as you ensure that the load on the carbon does not hit the critical stress point then the fatigue behaviour is super – it’s the best you can have. This was ensured by our whole testing process. There has not been a single failure of production VCLS seat post that I know of. "
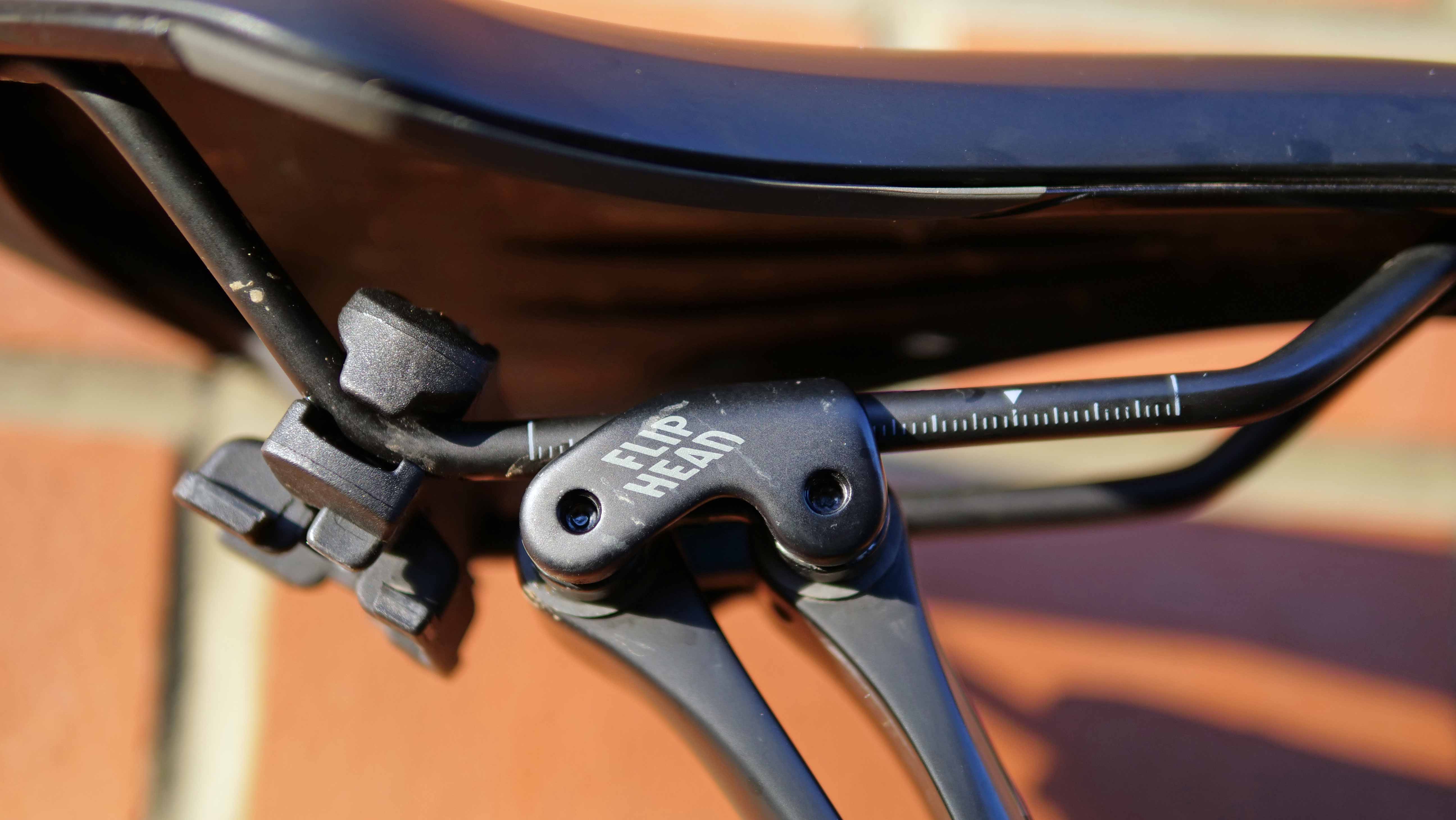
We asked Michael next about future plans for VCLS. As the design is essentially unchanged over the past ten years, do Canyon have plans for future updates? “Things are always changing in the cycling world. Design of bikes is changing. Many new gravel and road bikes no longer take a simple round cylindrical seatpost, so we need to find new interpretations of the VCLS concept with new shapes. In the end, the VCLS concept with stiffness where you want it and comfort where you need it, is a basic Canyon concept behind many of our bikes’ designs. You can achieve VCLS in many different ways. The great thing with the VCLS seatpost design is that it used the higher flexibility of the split design, with two leaf springs, but also combined it with the ‘flip head’ parallelogram mechanism with the two hinges at the head to avoid unnecessary rearward movement of the saddle. With a cylindrical design of seatpost this works really well, but now that seatpost shapes are changing, because of aerodynamic improvements or for other reasons, we will need to find new interpretations of the VCLS seatpost in the future. ”
Thanks to Michael Adomeit, Canyon’s Engineering Team Leader, for his great insight into the VCLS design and testing process.